Зона загрузки (или зона питания) играет важную роль в процессе экструзии. Тип и геометрия такой зоны заслуживает не меньшего внимания при конфигурировании экструзионной установки, чем, например, соотношение L/D, наличие смесительных секций, тип гребней и другие параметры. При рассмотрении конструкции зоны загрузки следует обратить внимание на две характеристики: тип и геометрия системы охлаждения, а также использование гладкой или рифленой геометрии цилиндра в этой части экструдера.
Назначением системы охлаждения зоны загрузки является создание термического барьера для предотвращения слишком быстрого размягчения поверхности полимерных гранул, повышения их липкости и, как следствие, появления «мостиков» (bridging) на стенках загрузочного окна. Образование «мостиков» приводит к снижению эффективной площади окна транспортировки полимера внутри материального цилиндра, дальнейшему его закупориванию и остановке процесса. Если такая ситуация возникает при работающем экструдере и равномерной подаче экструдата из фильеры, экструдат внезапно перестает вытекать из фильеры, при этом шнек продолжает вращаться, а уровень полимера в загрузочном бункере остается полным. Шнек, согласно показаниям датчика оборотов, по-прежнему вращается с заданной скоростью, но нагрузка на двигатель значительно снижена или почти равна нулю.
Температура в первой зоне экструдера имеет решающее значение для обеспечения необходимых характеристик расплава. Если температура в зоне 1 слишком высокая, преждевременное расплавление может привести к образованию смазывающей пленки на стенках цилиндра, что уменьшит трение между стенками цилиндра и полимером и приведет к скольжению пластика. Если температура в зоне 1 слишком низкая, трение между полимером и стенкой цилиндра также снижается за счет пониженной площади соприкосновения, что затрудняет транспортировку твердых частиц. При идеальной температуре в зоне 1 поверхность гранул становится липкой, что создает высокое трение, способствующее продвижению полимера вперед при вращении шнека.
Кроме того, зона загрузки является препятствием для передачи тепла от материального цилиндра на редуктор. Эта функция повышает надежность и эффективность контроля и управления передачей крутящего момента от привода на шнек.
Охлаждаемая зона загрузки может иметь два типа исполнения: встроенная и независимая.
Встроенная и независимая зоны загрузки
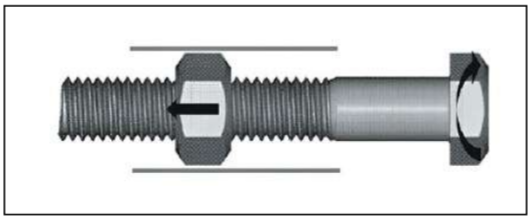
Рисунок 1. Модель транспортировки полимера в экструдере
В случае встроенного варианта загрузки материальный цилиндр является монолитным изделием, в необходимом месте которого выполнено отверстие для установки загрузочных устройств и подачи полимерного сырья. Система охлаждения представляет собой простую «рубашку», смонтированную на поверхности зоны загрузки или, в лучшем случае, комбинацию отверстий внутри стенки цилиндра.
Зона загрузки является независимой, если элемент материального цилиндра, предназначенный для подачи полимерного сырья, — это отдельный узел. Геометрия его каналов охлаждения часто имеет более сложную конфигурацию для повышения эффективности охлаждения, а в местах соединения с материальным цилиндром устанавливается дополнительная теплоизоляция. При использовании независимой зоны загрузки повышается уровень контроля и управления температурой в зоне загрузки со стороны оператора производственной линии, увеличивается эффективность автоматизации и обратной связи в системах автоматического управления экструзией.
Производители экструдеров, предлагающие встроенную конструкцию зоны загрузки, утверждают, что такая конструкция обеспечивает улучшенную соосность между цилиндром, шнеком и редуктором. Несоосность основного корпуса и зоны загрузки может вызвать проблемы, однако отсутствует какая-либо подтвержденная информация о том, что шнек застревал в корпусе экструдера по такой причине. Важно помнить, что шнек поддерживается и центрируется в цилиндре гидравлически за счет внутреннего давления полимера.
Функция транспортировки и предпластикации
Для понимания принципа транспортировки материала в экструдере можно использовать аналогию движения гайки по винту (рис. 1). В этом примере гайка выступает в роли полимерного слоя, а винт — в роли шнека. Для перемещения гайки коэффициент трения между пальцами (стенкой материального цилиндра) гайкой должен быть больше коэффициента трения между гайкой и винтом. По этой причине внутренняя поверхность цилиндра более шероховатая, а иногда и содержит специальные дополнительные каналы для увеличения коэффициента трения. Шнеки, с другой стороны, всегда имеют гладкую (отполированную) поверхность, чтобы сохранить коэффициент трения на как можно более низком уровне.
Рисунок 2 . Зависимость производительности экструзии и коэффициента трения между полимером и стенкой материального цилиндра
Типичные значения коэффициента трения между поверхностью цилиндра и полимерным материалом составляет 0,4, а между шнеком и материалом — 0,25. Эти значения зависят от давления, температуры, состояния поверхности (новая, старая, изношенная), наличия смазочных материалов или добавок в зоне загрузки и транспортировки, типа подаваемого материала (например, гранул, порошка или хлопьев), формы гранул и их размера, поверхности гранул (гладкой или шероховатой). В связи с большим количеством влияющих факторов сложно прогнозировать и управлять физическими процессам в этой зоне без применения специальных методов.
При повышении коэффициента трения между гранулятом и стенкой цилиндра возрастает скорость его перемещения в осевом направлении, то есть увеличивается экструзионная производительность (при одновременной реализации возможности соответствующей скорости пластикации в зоне сжатия). На рис. 2 показана зависимость между производительностью и коэффициентом трения.
Рисунок 3. Варианты геометрического исполнения канавок
При низком показателе коэффициента трения скорость перемещения гранулята резко меняется при небольших изменениях коэффициента трения. Процесс является статистически неуправляемым, даже небольшие изменения условий процесса либо в загрузочной горловине, либо в зоне 1 экструдера могут привести к существенным различиям в производительности. Кроме того, высокий коэффициент трения между полимером и шнеком приводит к так называемому переплавлению или пробке из расплава (полимер, расплавленный в зоне одного или нескольких витков в зоне подачи, который блокирует дальнейшую транспортировку материала).
Таким образом, возможны три следующих варианта перемещения гранул внутри экструдера:
— гранулят подается не в осевом направлении, а по траектории вращения вокруг шнека. В этом случае силы трения между гранулятом и шнеком намного больше, чем силы трения между гранулятом и цилиндром;
— гранулят подается исключительно в осевом направлении и не вращается вместе со шнеком. В этом случае силы трения между цилиндром и гранулятом намного больше, чем силы трения между гранулятом и шнеком. Такой вариант возможен только при использовании цилиндрических экструдеров с канавками и только в том случае, если геометрия канавок позволяет полностью предотвратить круговое перемещение;
— гранулят перемещается в осевом направлении, но также имеет место вращательное движение. Этот вариант обычно применяется на практике. Гранулят подается в осевом направлении, но при этом по-прежнему движется по круговой траектории. Таким образом, гранулы перемещаются по спиральной траектории от входного отверстия экструдера к фильере.
Возможны несколько вариантов исполнения геометрии канавок (рис. 3).
В научных публикациях нет единого мнения о том, какой вид канавок более эффективен для экструзии. Для более жестких и тугоплавких материалов, таких как полиамид, рекомендуется использовать осевые канавки закругленного профиля максимальной глубиной 0,5 мм (для шнека диаметром 60 мм). При превышении этих параметров наблюдается резкий рост нагрузки на привод экструдера. Для материалов, менее чувствительных к напряжению сдвига, таких как полиолефины, предполагается применение более глубоких и менее сглаженных канавок.
Рисунок 4. Суммарная длина зоны цилиндра со спиральными и осевыми канавками может составлять 2-4D
Для повышения эффективности применяется комбинация последовательного размещения спиральных и осевых канавок. Суммарная длина такой зоны может составлять 2-4D (рис. 4).
При прохождении гранулята через зону с канавками увеличивается трение между гранулятом и стенкой цилиндра. Это может привести к появлению дополнительного объема тепловой энергии, приводящего к повышению температуры стенки. В связи с этим возрастает роль контроля и управления эффективностью системы охлаждения, описанная выше.
Рисунок 5. Изменение давления по длине материального цилиндра
За счет такого дополнительного трения давление в экструдере возрастает сразу в зоне загрузки и далее уменьшается по мере продвижения материала по материальному цилиндру и повышения степени пластикации (рис. 5). Из-за смещения начала пластикации в зону загрузки иногда можно исключить зону сжатия из композиции шнека
Таблица 1. Преимущества и недостатки использования канавок в геометрии зоны загрузки
Рифленая зона загрузки наиболее эффективна при переработке ПЭНД и ПП для пленок, труб и выдувного формования (ПТР<3 г/10 мин), а также для переработки инженерных пластиков с повышенной производительностью. Она не подходит для очень твердых гранул, таких как ПЭТ, порошков (например, ПВХ), мягких термопластичных эластомеров и вторичных материалов. При смешивании суперконцентратов могут возникнуть проблемы ввиду недостаточного перемешивания. Преимущества и недостатки такой системы приведены в табл. 1.
ЛИТЕРАТУРА
1. Giles, Harold F.Extrusion: the definitive processing guide and handbook / by Harold F. Giles, Jr., John R. Wagner, Jr., Eldridge M. Mount, III. ISBN 0-8155-1473-5
2. J. Vlachopoulos and Nickolas D. Polychronopoulos. Understanding Rheology and Technology of Polymer Extrusion. First Edition, Polydynamics Inc, Dundas, ON, Canada (2019) ISBN 978-0-9952407-2-8
3. Screw and barrel design for grooved feed vs smooth bore extruders. Johannes Wortberg Gerhard-Mercator-University of Duisburg. Institute for Product Engineering — Engineering Design and Plastics Machinery Lotharstr. 1, D-47057 Duisburg, Germany
Автор:
Сергей Трифонов, директор испытательной лаборатории ООО «ПолимерФизик Руссланд», руководитель учебного центра ООО «Академия пластмасс»
Опубликовано в журнале "Пластикс" №5 /2024. Перепечатка возможна только с разрешения редакции журнала.